Intermediate Shaping Machine (With Manipulator)
Product Characteristics
● The machine is integrated with a reshaping machine and an automatic transplanting manipulator. Internal expansion, outsourcing, and shaping principle design of end compression.
● Controlled by an industrial programmable controller PLC; inserting a single mouthguard in each slot to arrange the enameled wire escape and flying; effectively prevent the enameled wire from collapsing, the bottom of the slot paper from collapsing and damage; effectively ensuring the shaping of the stator before binding Beautiful size.
● The height of the wire package can be adjusted according to the actual situation.
● The machine adopts a quick mold change design; mold change is quick and convenient.
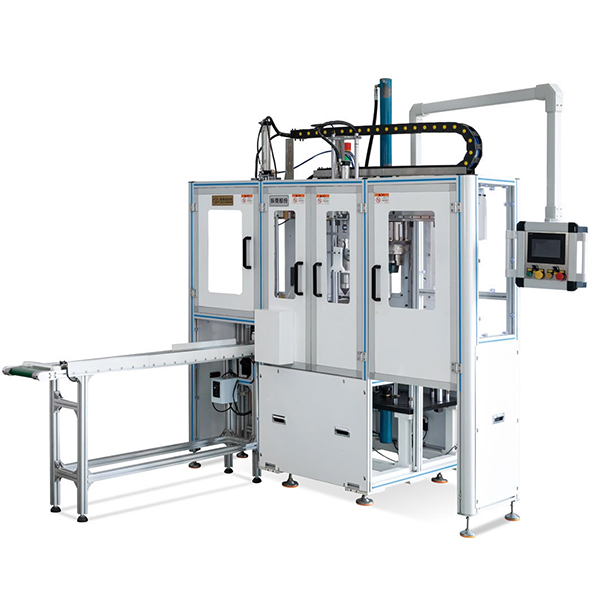
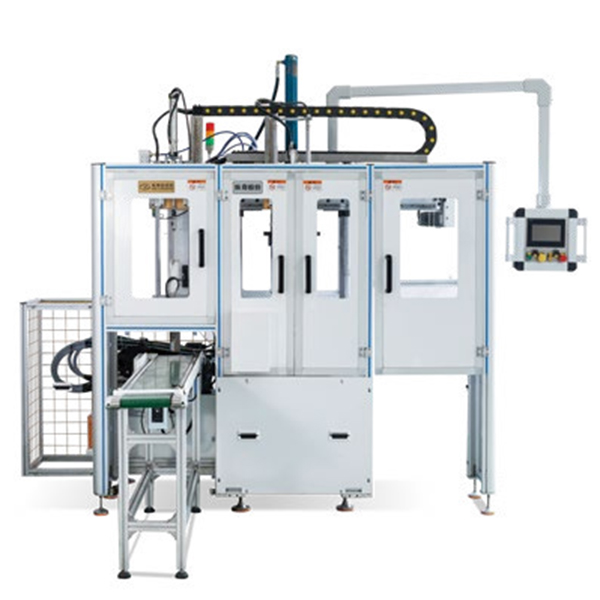
Product Parameter
Product number | ZDZX-150 |
Number of working heads | 1PCS |
Operating station | 1 station |
Adapt to the wire diameter | 0.17-1.2mm |
Magnet wire material | Copper wire/aluminum wire/copper clad aluminum wire |
Adapt to the stator stack thickness | 20mm-150mm |
Minimum stator inner diameter | 30mm |
Maximum stator inner diameter | 100mm |
Air pressure | 0.6-0.8MPA |
Power supply | 220V 50/60Hz (single phase) |
Power | 4kW |
Weight | 1500kg |
Dimensions | (L) 2600* (W) 1175* (H) 2445mm |
Structure
1. Important Considerations
- The operator should have full knowledge of the machine's structure, performance and usage.
- Unauthorized individuals are strictly prohibited from using the machine.
- The machine must be adjusted every time it is parked.
- The operator is prohibited from leaving the machine while it is running.
2. Preparations before Starting Work
- Clean the working surface and apply lubricating grease.
- Turn on the power and ensure that the power signal light is on.
3. Operating Procedure
- Check the direction of rotation of the motor.
- Install the stator on the fixture and press the start button:
A. Place the stator to be shaped on the fixture.
B. Press the start button.
C. Ensure the lower mold is in place.
D. Start the shaping process.
E. Take out the stator after shaping.
4. Shutdown and Maintenance
- The working area should be kept clean, with temperatures not exceeding 35 degrees Celsius and relative humidity between 35%-85%. The area should also be free from corrosive gas.
- The machine should be kept dust-proof and moisture-proof when out of service.
- Lubricating grease must be added to each lubrication point before every shift.
- The machine should be kept away from sources of shock and vibration.
- The plastic mold surface must be clean at all times and rust spots are not permitted. The machine tool and working area should be cleaned after usage.
- The electric control box should be checked and cleaned every three months.
5. Troubleshooting
- Check the fixture position and adjust if the stator is deformed or not smooth.
- Stop the machine if the motor rotates in the wrong direction, and switch the power source wires.
- Address issues that arise before continuing machine operation.
6. Safety Measures
- Wear appropriate protective gear such as gloves, goggles, and earmuffs to avoid injury.
- Check the power switch and emergency stop switch before starting the machine.
- Do not reach into the molding area while the machine is running.
- Do not disassemble or repair the machine without authorization.
- Handle stators with care to avoid injuries from sharp edges.
- In the event of an emergency, press the emergency stop switch immediately and then deal with the situation.