Three-Head Six-Station Vertical Winding Machine
Product Characteristics
● Three-head six-station vertical winding machine, three-station working and three-station waiting; mainly suitable for winding three-phase motor coils.
● Stable performance, atmospheric appearance; fully open design concept, easy to debug.
● This machine is suitable for stator winding with high output requirements; automatic winding, automatic segment skipping, automatic processing of bridge wires, automatic trimming, and automatic indexing are completed in sequence at one time.
● The man-machine interface can set the number of turns, winding speed, sinking height, sinking speed, winding direction, cup angle, etc.; winding tension is adjustable, bridge line processing is fully servo controlled, and the length can be adjusted arbitrarily ; It has the functions of continuous winding and discontinuous winding.
● Low energy consumption, high efficiency, low noise, long life and easy maintenance.
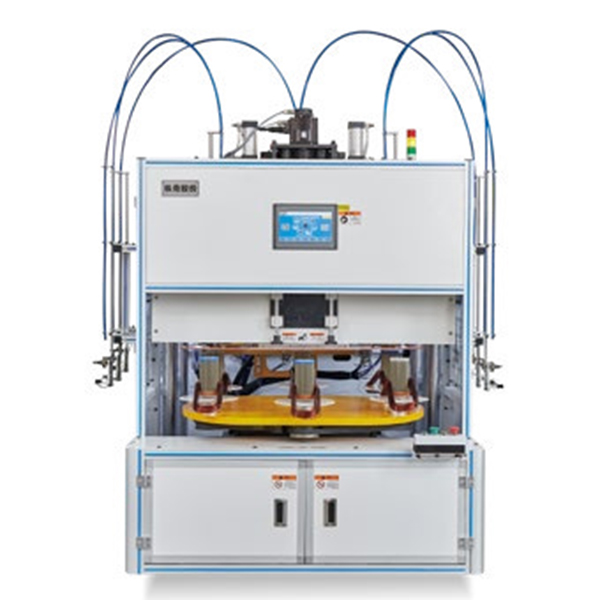
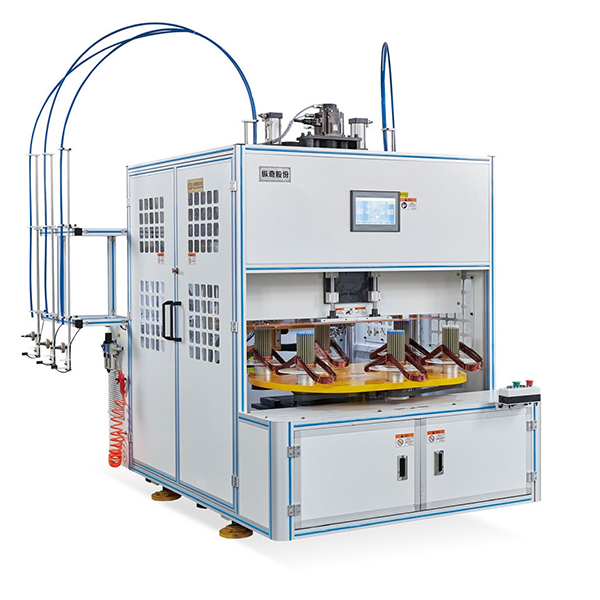
Product Parameter
Product number | LRX3/6-100 |
Flying fork diameter | 240-400mm |
Number of working heads | 3PCS |
Operating station | 6 stations |
Adapt to the wire diameter | 0.17-1.2mm |
Magnet wire material | Copper wire/aluminum wire/copper clad aluminum wire |
Bridge line processing time | 4S |
Turntable conversion time | 1.5S |
Applicable motor pole number | 2、4、6、8 |
Adapt to the stator stack thickness | 20mm-120mm |
Maximum stator inner diameter | 100mm |
Maximum speed | 2600-3000 circles/minute |
Air pressure | 0.6-0.8MPA |
Power supply | 380V three-phase four-wire system 50/60Hz |
Power | 10kW |
Weight | 2200kg |
Dimensions | (L) 2170* (W) 1500* (H) 2125mm |
FAQ
Problem : Diaphragm Issue Diagnosis
Solution:
Reason 1. Insufficient negative pressure on the detection meter can prevent the set value from being reached and cause a lack of signal. Adjust the negative pressure setting to an appropriate level.
Reason 2. The diaphragm size may not match the diaphragm fixture, preventing proper function. It is recommended to use a matching diaphragm.
Reason 3. Air leakage in the vacuum test may be caused by the diaphragm or fixture placement. Properly position the diaphragm, clean the fixture, and ensure everything is installed correctly.
Reason 4. Blocked or faulty vacuum generators can reduce suction and negatively impact negative pressure values. Clean the generator to resolve the issue.
Problem: When playing a sound film forward and backward, the air cylinder only moves up and down.
Solution:
When the sound film advances and retreats, the cylinder sensor detects a signal. Check sensor location and adjust if necessary. If the sensor is damaged, it should be replaced.
Problem: Diaphragm fixture continues to register load even with no diaphragm attached, or three diaphragms in a row without alarm.
Solution:
This problem can be caused by two possible reasons. First, the vacuum detector may be set too low to detect the signal from the material. This problem can be solved by adjusting the negative pressure value to an appropriate range. Second, the vacuum and generator may be blocked, resulting in insufficient pressure. To ensure optimum function, regular cleaning of the vacuum and generator systems is recommended.