Motor stator automatic production line (robot mode 2)
Product Description
● The robot is used to transfer the coils of the vertical winding machine and the ordinary servo wire inserting machine.
● Saving the operation labor of winding and inserting wires.
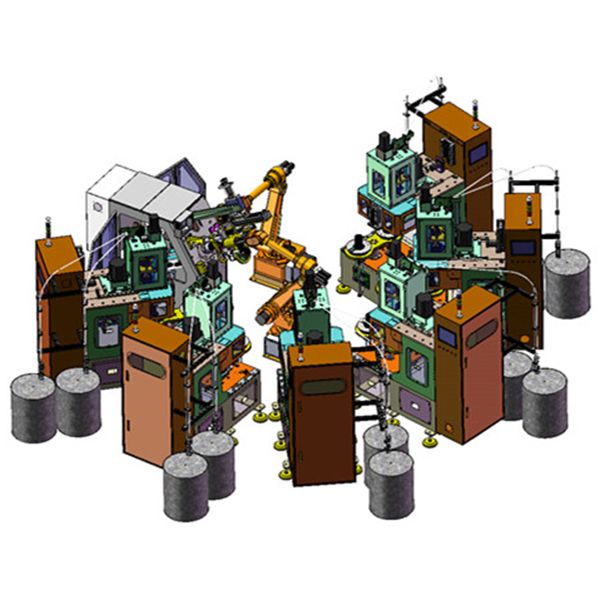
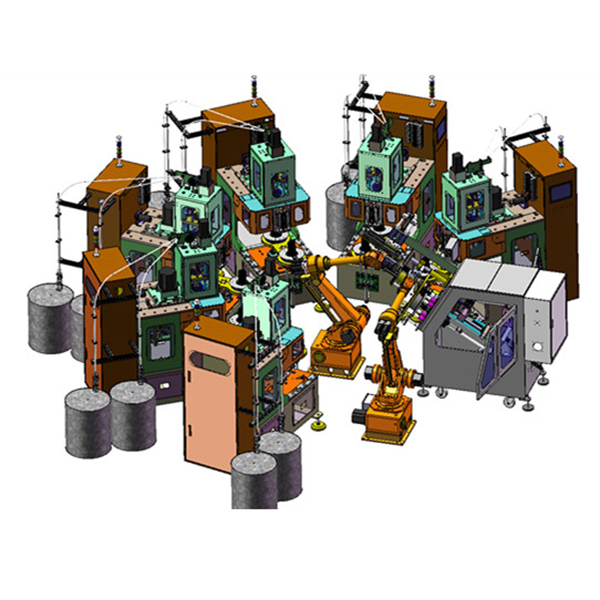
Structure
Solutions to common problems after rotor automatic line assembly
The rotor automatic line assembly is an automatic equipment composed of actuators, sensor elements, and controllers. Faults in the rotor automated assembly line can result in erratic or completely non-operational operation. In this article, we discuss four common methods for identifying faults in automatic rotor assembly lines.
1. Conduct a comprehensive inspection of the power supply, air source, and hydraulic source equipment in the rotor automatic line assembly. Most of the problems of the rotor automatic assembly line come from the problems of power supply, air source and hydraulic source. When checking, make sure that the power supply of the workshop is sufficient and that all equipment is powered normally. Check the air pressure source and hydraulic pump required for assembly line hydraulics.
2. Check whether the position of the sensor in the rotor automatic line assembly has changed. Over time, sensors may experience sensitivity issues, malfunction, or change in position. The detection position and sensitivity of the sensor must be checked frequently, adjusted properly when the position changes, and replaced immediately when it fails. Vibration problems during rotor moving assembly line operations can also cause loose sensors. It is critical to confirm that the sensor is firmly in place.
3. Check the relay, flow control valve and pressure control valve. The function of the relay is similar to that of a magnetic induction sensor, and long-term grounding problems will affect the normal use of the circuit and need to be replaced. The pneumatic or hydraulic system of the assembly line, the opening of the throttle valve, the pressure adjustment spring of the pressure valve, etc. will lose firmness or slip due to vibration problems, and require frequent maintenance during normal use.
4. Check electrical, pneumatic and hydraulic circuit connections. If the fault location check does not reveal the source of the problem, check the circuit status of the device for an open circuit. Verify that the wireway conductors are not contoured due to pull-out issues and inspect the bronchus for any damage or wrinkles. Check if the hydraulic oil circuit is blocked. If the trachea is severely wrinkled, it should be replaced immediately. If there is a problem with the hydraulic oil pipe, it will also need to be replaced.
5. If the above conditions do not exist, the probability of program problems in the rotor automatic line controller is relatively low.